VJ Instruments'
Lab-Scale Rapid Mixer Granulator: Perfect for Small-Scale Granulation Trials
Revolutionizing Granulation: The VJ Instruments Lab Model Rapid Mixer Granulator
Application
General Structure & Mountings
Mounting frame is made out of mild steel & SS304 and M.S. parts cladded or covered with SS304, in which drive assembly is mounted at the bottom. This frame is covered with SS304 sheet. Mixing bowl is mounted at the top of this frame. Mounting platform is covered with SS304 covers from all sides. Staircase & railings are not required in 10 Lit.
Mixing Container
Mixing container (bowl), in which contact parts are made out of SS316 quality material. It comprises a flat base with a lower vertical cylindrical wall section and an upper conical section. A conical bowl is the natural shape for difficult materials. Light dusty powders do not float unmixed on the surface of the circulating vortex. Wet granulations do not stick to the walls, but discharge cleanly from the bowl with no product loss. Specially designed bowl is provided with lid which is having a vent, view and charging ports. Main impeller’s drive shaft is mounted directly on output shaft of the worm reduction gear box. The seal housing at main stirrer’s drive shaft may be flushed with cleaning water, which is then drained away from the machine through built in drain tubes. A high speed granulator is inserted horizontally through wall of bowl to assist blending of powder and to break the product to the granules of the required size. The seal housing at drive shaft of granulator also flushed with cleaning water, which is then drained away from the machine through built in drain tubes.
Special Features
The discharge port is mounted horizontally in to the bowl with vertical downward opening. This discharge port is operated by pneumatic cylinder in . A discharge valve, which is built horizontally in to the wall of the bowl and is operated from the operator’s control panel in bowl. A T/C clamping system gives unrestricted access into the chute for easy cleaning. All internal and external surfaces of the discharge valve are of polished stainless steel and very easy to clean. The design of discharge port will be flush type, which flush with inner surface of the container. Due to this design no pocket will develop at the discharge port.
Control Panel and Pneumatic system
The operating panel will be mounted on platform and is provided with following controls, in
electrically controlled panel.
• Three/Single phase indicating lights.
• Variable speed of Impeller motor & Slow & Fast speed of Chopper motor.
• Pneumatic/Manual controls for the opening and closing of the discharge port.
• Ammeters for both motors (Optional).
• Main panel provided with pressure switch control for proper functioning of machine at
desired air pressure.
• The system Consist of moisture & Oil separator with regulator, pressure gauge, air
regulator, solenoid valve and required pipes and pipe fittings.
Discharge Port
• Homogeneous binder distribution.
• Short batch time and reduce cleaning time.
• Maximise cleaning effectiveness.
• Inbuilt Air Purging system/Manual
• Air purge sealing system for Impeller shaft and Chopper shaft. (Dry oil free air will be
provide by customer up to machine)
• All product contact parts are made out of SS 316 & polished to the mirror finish.
• A high-speed chopper is inserted horizontally through wall of bowl to assist blending of
powder and to break the product to the granules of required size.
• A high speed chopper is inserted horizontally through wall of bowl to assist blending of
powder and to break the product to the granules of un-even size. (Wet Granules).
• Chopper motor is provided with a removable stainless steel shroud, which covers the motor
and simplify cleaning.
• All moving part of the machine are totally enclosed to eliminate accident.
• The machine can-not be started unless and until the mixer cover is properly closed.
• Flush wall type discharge valve eliminates pockets at the port of discharge valve.
• Pneumatically operated (non-rotating type) material discharge valve for 5Kg containers.
• Castor wheel mounted mobile unit for easy handling (Optional).
• Top cover with facility of light glass, sight glass and air filter .
• Stainless steel air receiver.
• Air filter for compressed air.
• Granulator with U shape & knife edge blades
• Binder spraying facility with Tank facilitated with Stirrer & Spray Nozzle (Optional).
• A.C. Frequency drive for variable speed of Chopper.
• Manual/PLC based power panel & touch screen based operating panel.
Technical Specification
Sr. No. | Specification | Details |
---|---|---|
1 | Model No. | VJRMG |
2 | Certificate | GMP, ISO, CE |
3 | Purpose / Application | Homogeneous mixing of dry & wet powders, deagglomeration of wet mass and fast dispersion of binding agent. |
4 | Type | Standard Unit GMP Model |
5 | Working Volume | 0.5 Liters, 3 Liters, 5 Liters & 10 Liters or any specific dimension up to 0.5 L to 10 L. |
6 | MOC | Contact part SS316 & Non-contact part SS304 |
7 | Discharge | Nylon / SS316 |
8 | Discharge port | Manual / pneumatic |
9 | Operation | Manual / Through HMI |
10 | Bowl Test pressure | Water fill up, this test for weld joints only. Discharge assembly is not necessarily watertight. |
11 | Quality Assurance | Design, manufacture, installation & documentation in accordance with Good manufacturing practice. |
12 | Finish | Product contact parts internally finished to minor. Externally finished to dull matt. |
13 | Electrical rating | Non FLP, 2.2 Kw, 415V, 50 Hz, 3-phase |
14 | Impeller Type | Single speed, Crompton / Hindustan or std. make. |
15 | Impeller Motor | 2HP / 1440 RPM |
16 | Seal of Main Impeller | Mechanical seal with Air Purging |
17 | Impeller Gear Box | Ratio 10:1 Make – Standard Make. |
18 | Mounting | Inverted outshaft, Projecting upward. |
19 | Chopper type | Single speed Crompton / Hindustan or std. make. |
20 | Chopper motor | 2880 RPM/ 0.75 HP |
21 | Sealing of chopper | Gland seal with air purging |
22 | Mounting | Flange Mounted |
23 | Bearing Housing | The bearing housing of the main shaft connected to gearbox. Chopper blade assembly consists of a separate bearing housing coupled to motor with telescopic universal joint |
24 | Mixing Bowl | The mixing bowl is cylindrical with a large diameter and flat base. The top portion of the bowl is conical in shape to assist circulation of cohesive powders. The bowl is fabricated from SS316 Quality stainless steel with all internal and external surfaces polished to mirror finish. |
25 | Lid lifting system | Manual open able type, lid consists of charging hole with ball valve manually operated, air filter and special type of silicon gasket. |
26 | Impeller Mixing blade | Impeller mixing blade consisting of three nos. specially designed for intense mixing. The angles of the blades are such that the continuous action of this with different ingredients immensely mixes thoroughly with homogeneity. Mixing blade assembly is mounted on the main shaft with a separate bearing housing which fully eliminates any chance of cross-contamination of product with any lubricants. The upper portion of the housing contains a specially designed Teflon seal along with air purging facility. The lower stage housing contains bearings along with oil seals that make it completely leak-proof. |
27 | Granulator / Chopper Blade | A high-speed granulator is inserted horizontally through the wall of the bowl to assist blending of powder and to break the lumps of the products into granules of required sizes. These lumps are formed while wet mixing. Following chopper profile can be offered as an option. Knife-edged, 2/4 bladed (depending on bowl Capacity) impeller. |
28 | Discharge Valve | Machine has a side discharge outlet with pneumatically operated or manual. The discharge valve is exactly machine the profile of the intervene bowl with a perfect sealing arrangement. The pneumatic cylinder housing is specially designed with a swivel-type arrangement, which helps for easy cleaning. Safety interlocks are provided to discharge valve as well as top lid with a limit switch. The machine will not operate if discharge is open at hing. |
29 | Discharge Size | As per drawing. |
30 | Discharge Height | As per drawing. |
31 | Discharge Length | As per drawing. |
32 | Main Base Stand | Rigid Machine base frame made from S.S. material designed to accommodate the mixing bowl and the control panel. The motor directly connected to the reduction gear box drive inside and the machine base. Removable SS cover finished matte finish on all sides of the machine base frame. |
33 | Electrical Control System | SS304, PLC controlled with HMI or Standard Manual Control |
34 | Electrical Function | ◉ Main Motor On/Off ◉ Chopper Motor On/off ◉ Emergency stop ◉ Ampere Display of Main and chopper Motor ◉ Process Time auto/Manual switch for main Impeller. |
35 | Location | Ergonomically mounted on stand. |
36 | Pneumatic System | The machine is supplied with duly required pneumatic systems of Standard make. The customer has to ensure the supply of oil-free compressed air, also free from any other impurity which may contaminate the product. Air Filter and Air-water separator are also provided with the machine. The pressure regulator is provided to regulate the desired air pressure. The systems are suitable to accept an input air pressure of 5kg/cm2 to be terminated at 1/4” BSP” terminal. Air lubricator is provided to lubricate solenoid valve and Pneumatic Cylinder is incorporated in the system. |
37 | Electrical | All Major switch gears like contractors, Relay, Motor protection breaches are from Standard make only. |
38 | Utility Requirement | ◉ Power Consumption 3Kw @415 V, 3 Phase, 50Hz. ◉ Filtered, Dry, Oil-Free compressed Air |
39 | Safety Features | ◉ Enclosed moving parts. ◉ Machine will not start with open lid. ◉ Machine will not start with open discharge valve from T/C clamping. ◉ Rapid Mixer Granulator is designed to achieve excellent mixing and consistent granules at lower operating costs along with higher productivity. Better mixing and closed control of granule size lead to faster tableting speeds with improved quality and least rejections. |
40 | Documentation | Design Qualification, Installation Qualification & Operation Qualification documents. Material test certificate for contact parts. Installation & maintenance manual spare part lit. Warranty certificate of the machine Certificates, Manual for Brought out items. Electrical Circuit Diagram Schematic Diagram of the machine showing overall GA & PID Diagram. |
41 | Quantity | 1 |
42 | Dimension with pan | 800 mm (L) X 500 mm (W) X 1100 mm (H) |
43 | Weight | 110 Kg (Approximate) 200 kg with packing (Approximate) |
Note: Capacities mentioned above depend on samples used and may vary accordingly. VJ Instruments product development is a continuous process so specifications may change without prior notification.
Safety Features
- Enclosed moving parts.
- Machine will not start with open lid.
- Machine will not start with open discharge valve from T/C clamping.
- Rapid Mixer Granulator is designed to achieve excellent mixing and consistent granules at lower operating cost along with higher productivity. Better mixing and closed control of granule size leads to faster tableting speeds with improved quality and least rejections.
Certifications
01.
CE Certificate
02.
GMP Certificate
03.
ISO Certificate
04.
MSME Certificate
Frequently Asked Questions
We understand that you may have questions about our Lab-Scale Rapid Mixer Granulator, its applications, and how it can benefit your specific needs. Here are some common questions and answers to provide you with quick and helpful information:
What is a pharmaceutical granulator machine and how does it work?
What are the advantages of using a rapid mixing granulator?
What is a rapid mixture granulator and why is it used in pharmaceuticals?
What are the benefits of using a lab scale granulator?
What should I consider when choosing granulator machine manufacturers in India?
What does an RMG manufacturer provide for pharmaceutical applications?
How do I choose the right Rapid Mixer Granulator for my production needs?
What are RMG machines and why are they important in pharmaceutical manufacturing?
What is the Rapid Mixer Granulator (Lab Model) by VJ Instruments
The Rapid Mixer Granulator is a revolutionary machine designed for handling smaller trial batches for granulation. It offers flexibility and cost benefits for various processing needs.
What is the general structure and mountings of the RMG Lab Model?
What materials are used for the mixing container (bowl)?
Are there any special features of the RMG Lab Model?
How is the control panel and pneumatic system configured?
Can you explain the discharge port and its benefits?
What safety features are incorporated into the RMG Lab Model?
How does the RMG Lab Model improve granule quality and productivity?
Are there any optional features available for this machine?
What are the electrical service requirements for the RMG Lab Model?
Does the RMG Lab Model require a specific foundation or platform for installation?
No, the RMG Lab Model is designed for self-foundation, making it convenient to set up and use.
What is the temperature range that the Temperature Controller of the RMG Lab Model can handle?
The Temperature Controller can control temperatures in the range of ambient to 80°C, providing versatility for various processing needs.
International Clients
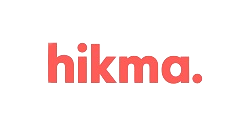



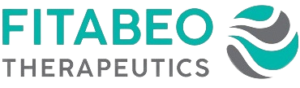
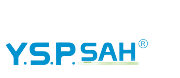
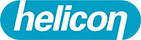
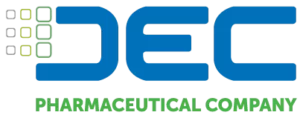
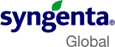
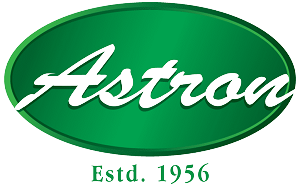
Industrial Clients
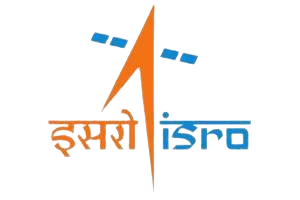
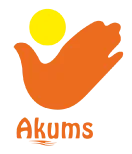
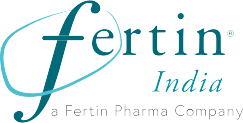
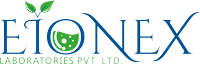
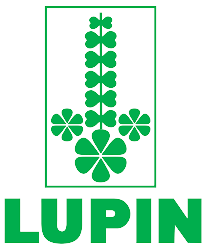
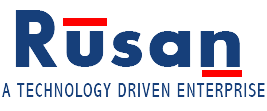
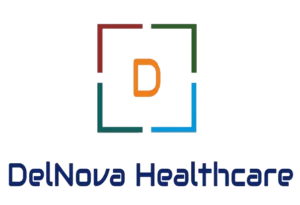
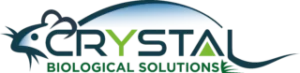
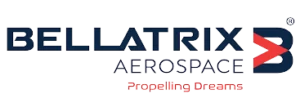
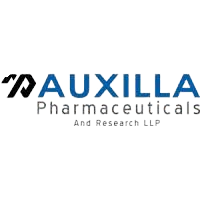
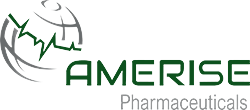
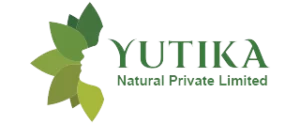
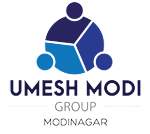
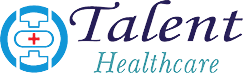
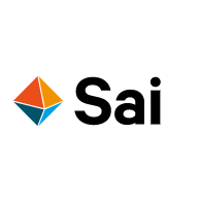
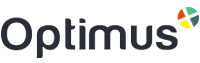
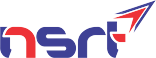
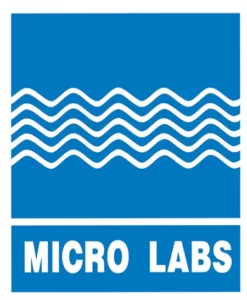
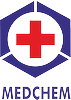
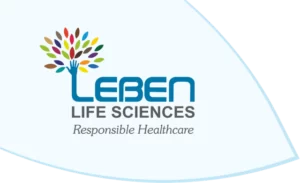
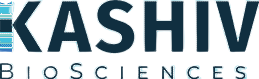
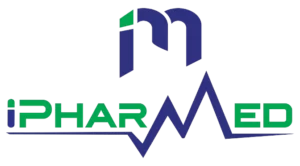
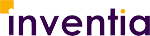
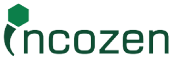
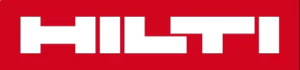
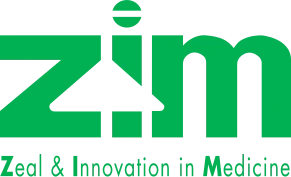
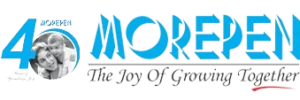
IITs, AIIMS, CSIR, Government and Private Institutes
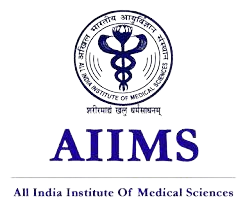
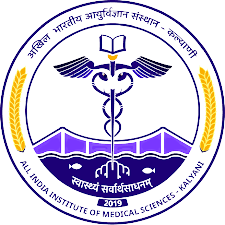
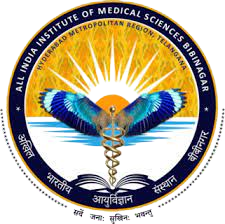
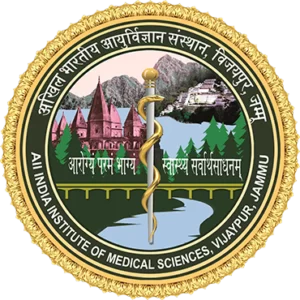
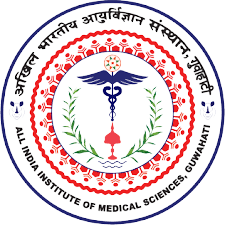
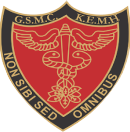
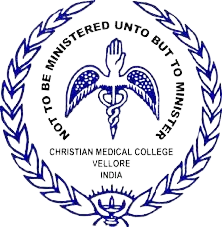
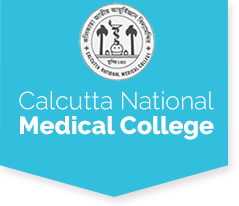
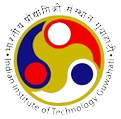
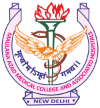
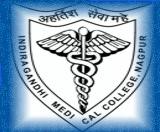
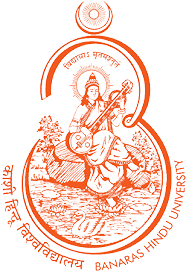
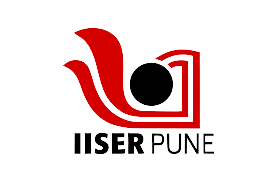
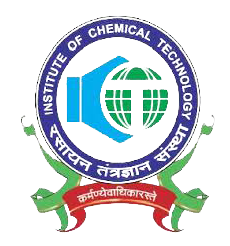
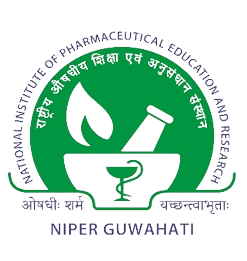
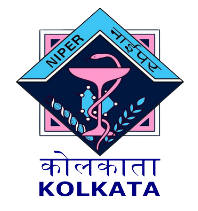
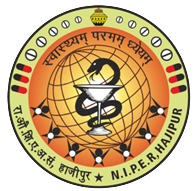
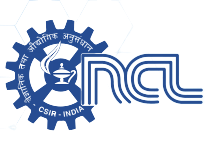
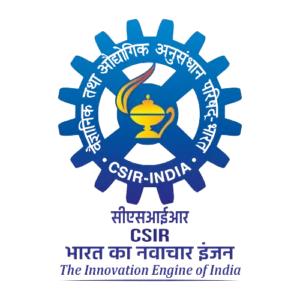
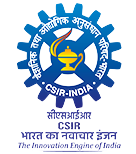
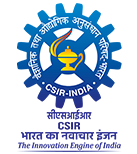
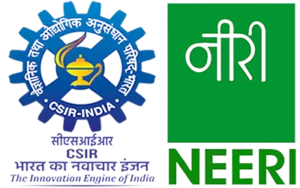
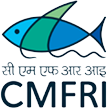
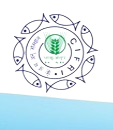

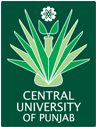

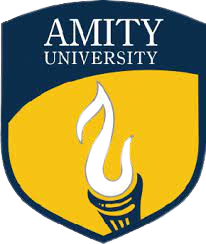
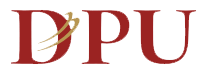
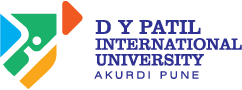
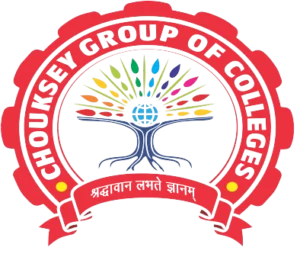
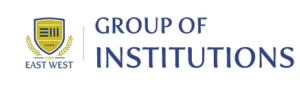
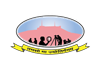
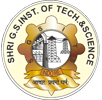
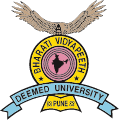
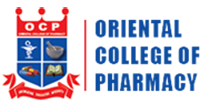
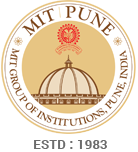
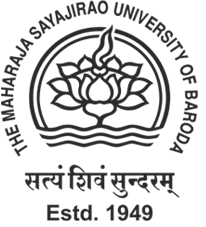

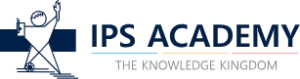
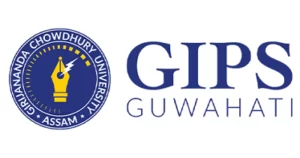
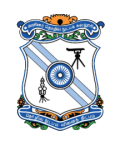
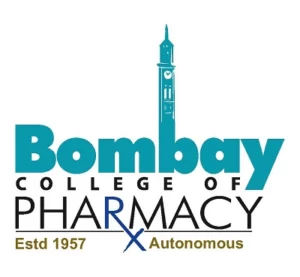
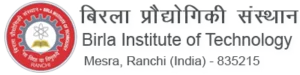
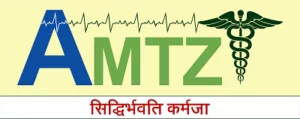
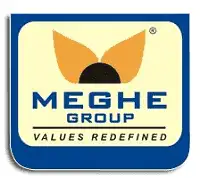
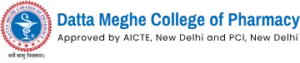
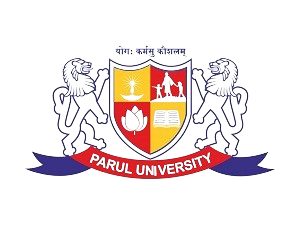
Related Products
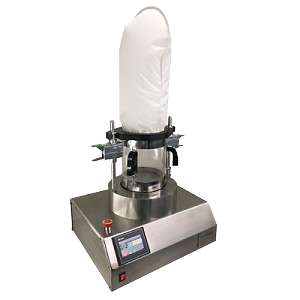
Lab-Scale Fluid Bed Dryer
VJ Instruments’ Lab-Scale Fluid Bed Dryer: Precision Drying for Research and Development Welcome to our
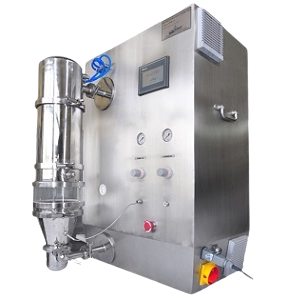
Fluidized Bed Processor
VJ Instruments’ Fluidized Bed Processor: Revolutionizing Research and Development Welcome to the world of innovation
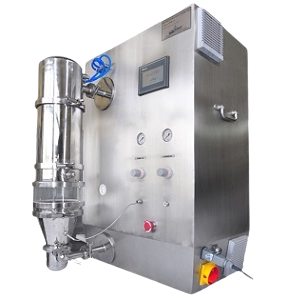
Fluid Bed Top Coater
VJ Instruments’ Revolutionizing Coating and Drying: Introducing the Fluid Bed Top Coater VJ Instruments proudly

R&D Tablet Coater
VJ Instruments’ Efficient Small-Batch Tablet Coating Solution for Pharmaceutical R&D The Pharma R&D Tablet Coater