VJ Instruments'
Fluidized Bed Processor: Revolutionizing Research and Development
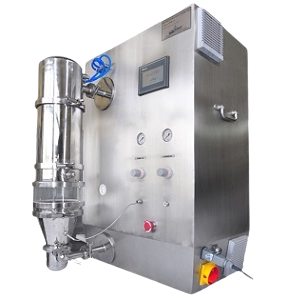
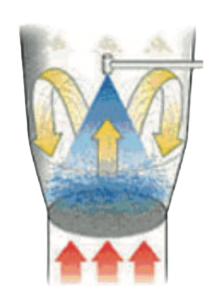
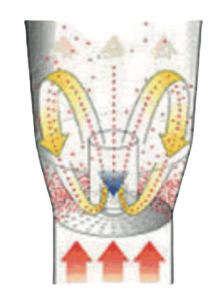
Discover the Magic Behind the Fluidized Bed Processor
Application
The Fluidized Bed Processor by VJ Instruments is a versatile solution tailored for the research and development needs of various industries, including pharmaceuticals, chemicals, food production, and academic institutions like pharmacy colleges. Its primary functions involve coating and drying pellets, allowing for a wide range of applications, such as:
- Color Modification: Altering the color of pellets for specific requirements.
- Improved Taste: Enhancing the taste of pharmaceutical or food products.
- Modified Release: Achieving controlled and modified release forms.
- Moisture and Oxygen Protection: Safeguarding products from environmental factors.
The Problem
Traditionally, research and development units in pharmaceutical companies were constrained by the limitations of existing coating facilities. This forced them to manufacture unnecessarily large quantities of test drugs, resulting in significant waste of effort and resources.
The Solution
The Fluidized Bed Processor is designed to address this specific challenge by offering a unique standard for handling small batches of pellets. It ensures that the quantity of the test batch never exceeds your requirements, reducing waste and improving efficiency.
Key Benefits
- Versatile Coating: Capable of handling both aqueous and organic film coating systems.
- Portability: Extremely portable for ease of use and mobility.
- Advanced Control Panel: Allows for monitoring and recording of all settings for the Fluid Bed Processor.
Components and Features
Coating Cylinder/Container/Bowl
- Central cylindrical portion made of SS-316 quality material.
- Glass cylinder for easy viewing during the coating process.
Heater
- Heats the inlet air to the desired temperature required for drying pellets.
- Temperature can be controlled from ambient to 90°C.
Exhaust Pipe
- Clears unwanted fumes and dust generated during the coating process.
Spray Gun
- Designed for top and bottom spray coating.
- Utilizes SS-316 nozzles and peristaltic pumps for precise dosing.
- Adjustable for droplet size depending on the viscosity of the solution.
Control Panel
- 4-inch Touch Screen PLC-based advanced control panel for comprehensive control.
Peristaltic Pump
- Delivers an exact amount of solution to the spray gun through a silicone pipe.
Operation
Bottom-Spray Coating (Wurster Coating)
- Uses energy to create a pneumatic mass transport, ensuring uniform coating.
- Ideal for coating small particles with high coating quality.
- Prevents premature viscosity changes of the coating droplet.
Top-Spray Coating
- Suitable for both batch and continuous operations.
- Ensures good spreadability and quality coating.
Technnical Specification
FBP SPEC. | Model No. | VJFBP-01 |
---|---|---|
Interface | PLC | |
Electrical Services | As per country requirement | |
Peristaltic Pump RPM | 3 to 100 rpm | |
Spray Gun | SS316 1.0 mm Bore (for Top and Bottom Spray) | |
Temperature Controller | Ambient to 80°C | |
Temperature Sensor | PT-100 | |
Heater | 1 HP | |
Fluidised Air Blower | Compressor Air 7.5 Bar | |
Height | 860mm | |
Length | 710mm | |
Width | 400mm | |
Weight (Approx.) | 110 Kg | |
Foundation | Self | |
Capacities (may vary) | Dependent on samples used |
Safety Features
- Emergency stop switch.
- Auto stop feature when process time completes.
Certifications
01.
CE Certificate
02.
GMP Certificate
03.
ISO Certificate
04.
MSME Certificate
Frequently Asked Questions
We understand that you may have questions about our Fluidized Bed Processor, its applications, and how it can benefit your specific needs. Here are some common questions and answers to provide you with quick and helpful information:
What are the benefits of using a fluidized bed coater in pharmaceutical manufacturing?
A fluidized bed coater provides several advantages in pharmaceutical manufacturing, including uniform coating thickness, controlled release formulation capabilities, reduced process time, and improved product stability. It also supports aqueous and solvent-based coatings, ensuring compliance with strict industry regulations.
How do I select the right equipment for fluidized bed powder coating?
Selecting the right fluidized bed powder coating system depends on your production volume, part size, coating material, and required finish quality. VJ Instruments offers customizable fluidized bed systems designed to deliver consistent performance, energy efficiency, and compatibility with various powder types.
What is fluidized bed coating equipment and how does it operate?
Fluidized bed coating equipment is used to apply a uniform coating to particles, granules, or small components by suspending them in a stream of air while spraying a coating solution. This technique ensures even distribution, faster drying, and higher efficiency, making it ideal for pharmaceutical, chemical, and food processing industries.
What are the benefits of using a fluidized bed powder coating machine?
How do I choose the right lab scale fluid bed processor for my application?
What are the main applications of a fluid bed processor?
What are the benefits of using a fluid bed coating machine in pharmaceutical manufacturing?
What factors influence the fluid bed coater price?
What is the primary purpose of the Fluidized Bed Processor?
How does the Fluidized Bed Processor reduce waste in research and development?
What types of coatings can the Fluidized Bed Processor handle?
What are the safety features of the Fluidized Bed Processor?
Can I adjust the temperature for pellet drying in the Fluidized Bed Processor?
What is the capacity of the Fluidized Bed Processor, and can it be customized?
Is it possible to scale up results from a lab scale fluid bed processor to industrial production?
What are the primary applications of a fluid bed granulator?
International Clients
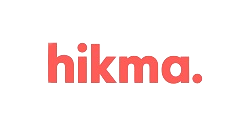



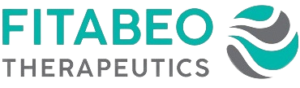
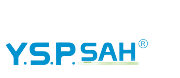
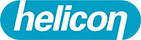
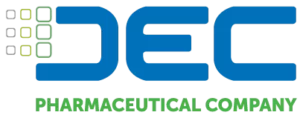
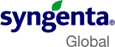
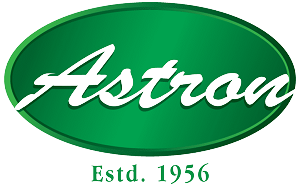
Industrial Clients
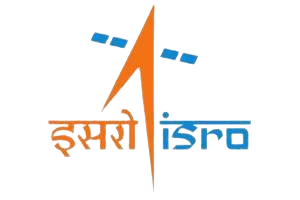
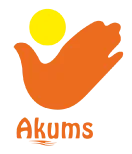
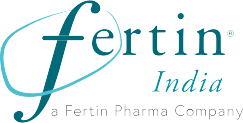
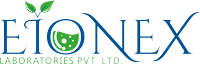
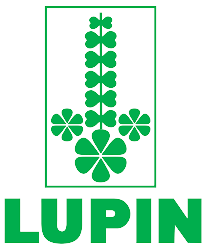
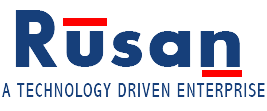
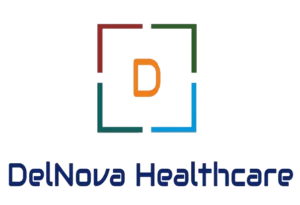
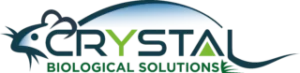
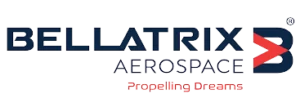
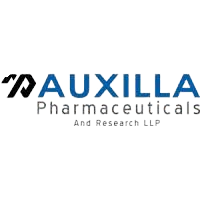
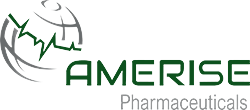
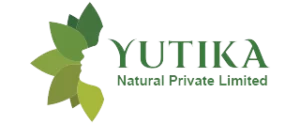
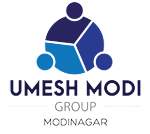
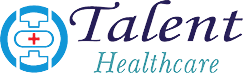
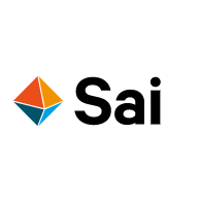
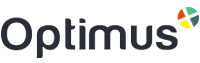
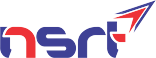
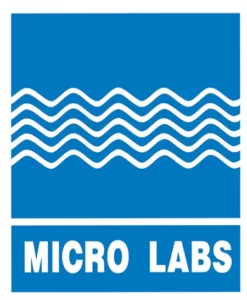
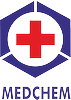
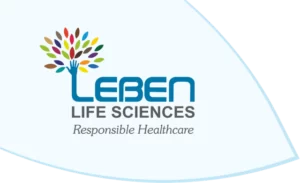
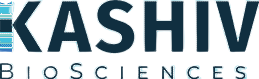
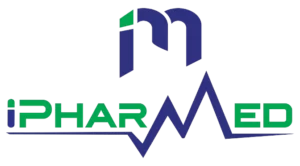
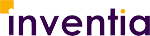
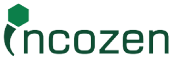
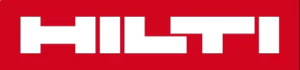
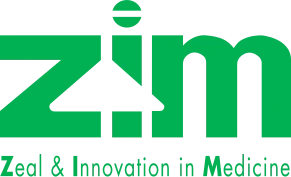
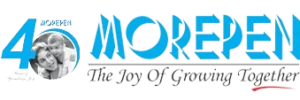
IITs, AIIMS, CSIR, Government and Private Institutes
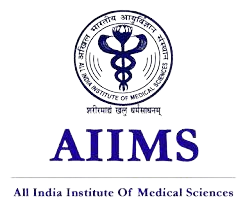
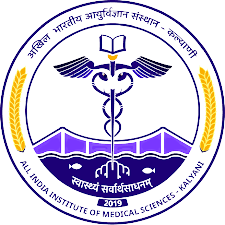
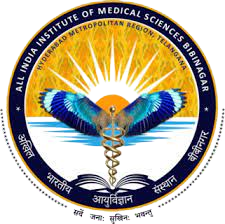
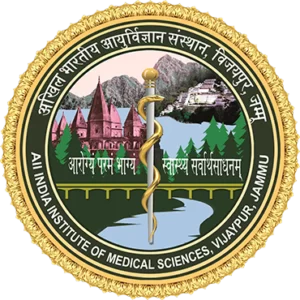
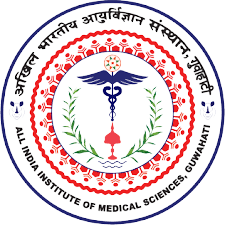
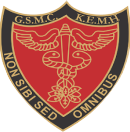
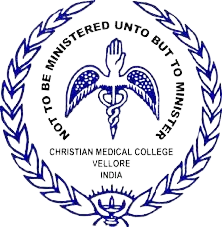
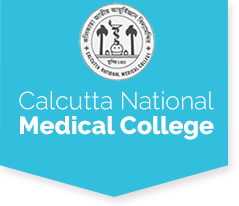
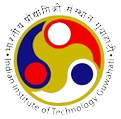
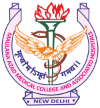
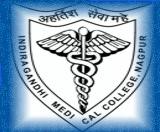
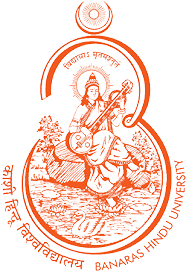
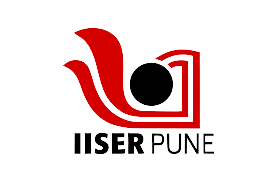
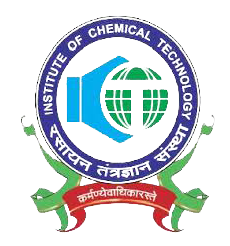
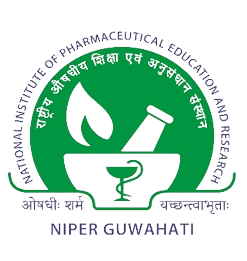
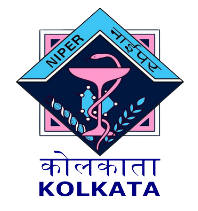
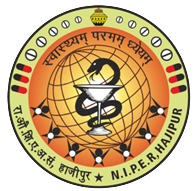
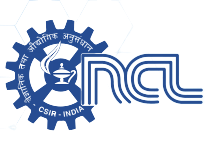
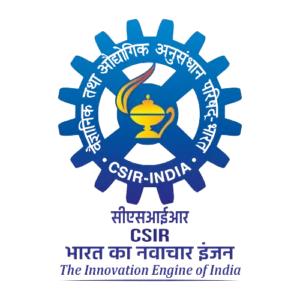
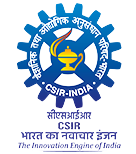
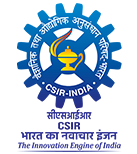
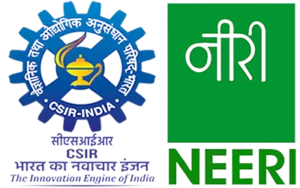
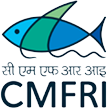
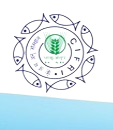

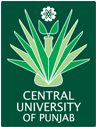

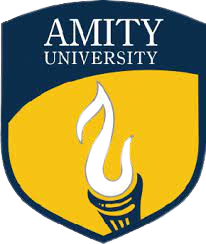
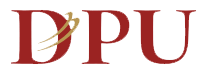
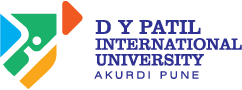
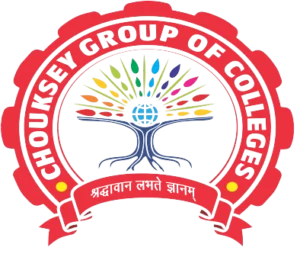
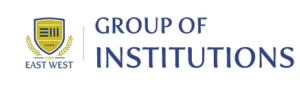
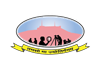
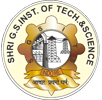
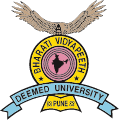
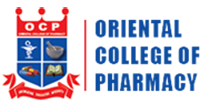
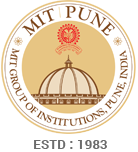
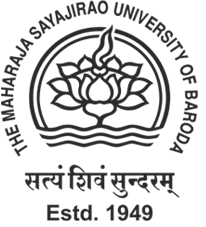

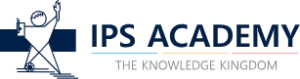
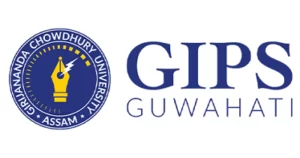
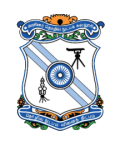
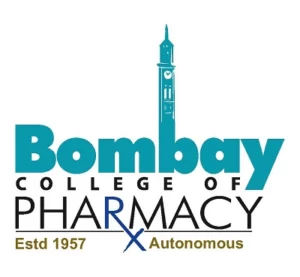
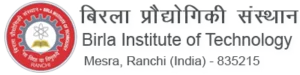
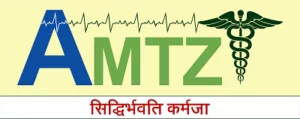
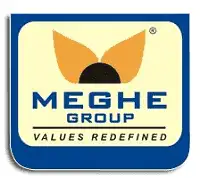
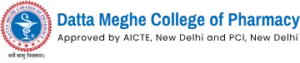
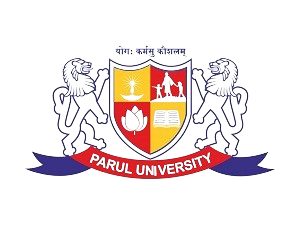
Related Products
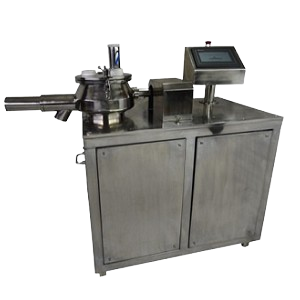
Lab-Scale Rapid Mixer Granulator
VJ Instruments’ Lab-Scale Rapid Mixer Granulator: Perfect for Small-Scale Granulation Trials Welcome to VJ Instruments,
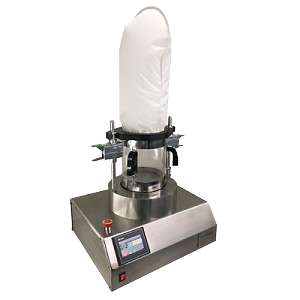
Lab-Scale Fluid Bed Dryer
VJ Instruments’ Lab-Scale Fluid Bed Dryer: Precision Drying for Research and Development Welcome to our
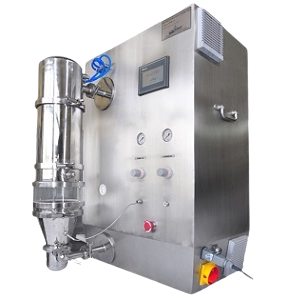
Fluid Bed Top Coater
VJ Instruments’ Revolutionizing Coating and Drying: Introducing the Fluid Bed Top Coater VJ Instruments proudly

R&D Tablet Coater
VJ Instruments’ Efficient Small-Batch Tablet Coating Solution for Pharmaceutical R&D The Pharma R&D Tablet Coater