VJ Instruments'
Die Roller Extruder: Precision Extrusion Made Easy
Unveiling the Magic: How the Die Roller Extruder Works
Application
Operation
The Die Roller Extruder features two horizontally placed rollers:
- Perforated Roller: This roller is responsible for creating perforations in the material.
- Knurling Roller: The knurling roller adds texture or specific patterns to the extruded material.
Here’s a step-by-step breakdown of how it works:
- Material is manually charged into the hopper.
- The hopper includes a drum and blade provision attached to a motor. This motor rotates and drives the material into the feeding hopper situated between the rollers.
- Due to the pressing nature of the rollers, the material is extruded through the perforations in the perforated roller.
This process results in precisely extruded material with the desired texture or pattern, making the Die Roller Extruder an indispensable tool for various applications.
Technical Specification
Sr. No. | Specification | Details |
---|---|---|
1 | Model No | VJDRE – 01 |
2 | Certificates | GMP, ISO, CE |
3 | Type | Single Screw |
4 | Production Capacity | 2-6 kg/hr depends on formulation. Minimum batch size: 100 g/batch (Approx). Maximum batch size 2kg. 0.5 kg/h (Minimum) – 2 kg/h (Maximum) capacity output on continuous batch. |
5 | Perforated mesh hole diameter | 1mm Standard. Optional 2.00 – 8.00 mm available with extra cost. |
6 | Product | Any Aqua base or solvent base formulation. |
7 | RPM of screw | 10 to 150 rpm |
8 | Hopper Discharge | Auto discharge by gravity |
9 | Electric Accessories | 440 V 3 Phase 50 Hz |
10 | MOC Contact Parts | SS 316 |
11 | MOC Non-Contact Parts | SS 304 |
12 | Hardware | Standard Make (Bearing shaft seal of SKF etc or equivalent) |
13 | Finish | Non-Contact Area Matt Finish Contact area Matt Finish Machine part- Machine Finish |
14 | VFD | Delta |
15 | Drive Motor | Crompton or equivalent |
16 | Reduction Gear Box | Impel or equivalent |
17 | Cutter arrangement for extruder | A blade cutter arrangement capable of cutting the extruded material to make granule of desired length |
18 | Documents | User Manual |
19 | Electric Consumption | 1 kWh |
20 | Dimension (LXWXH) in mm | 540 mm (L) X 565 mm (W) X 415 mm (H) |
21 | Weight | 85 kg. (Approximate) 150 kg. with packing (Approximate) |
Safety Features
- Emergency stop switch.
- Auto stop feature when process time completes.
Certifications
01.
CE Certificate
02.
GMP Certificate
03.
ISO Certificate
04.
MSME Certificate
Frequently Asked Questions
We understand that you may have questions about our Die Roller Extruder, its applications, and how it can benefit your specific needs. Here are some common questions and answers to provide you with quick and helpful information:
What is the primary purpose of the Die Roller Extruder?
What materials can be processed using the Die Roller Extruder?
How does the Die Roller Extruder work?
What are the key technical specifications of the Die Roller Extruder?
International Clients
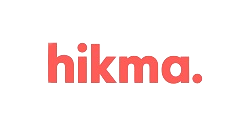



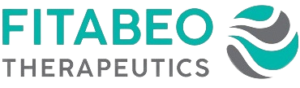
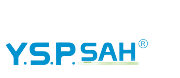
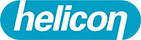
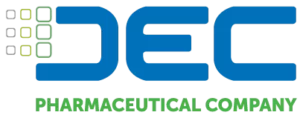
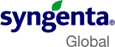
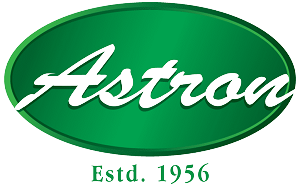
Industrial Clients
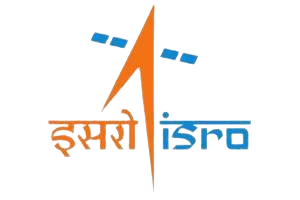
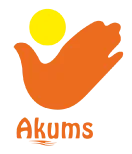
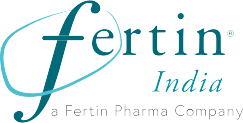
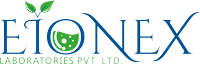
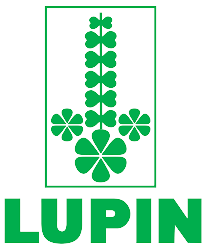
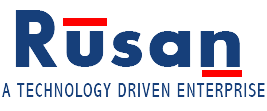
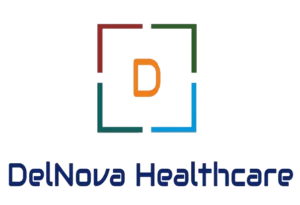
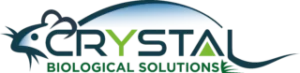
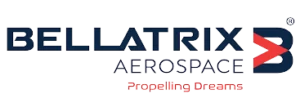
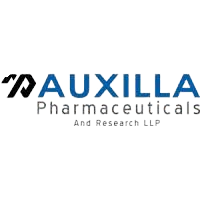
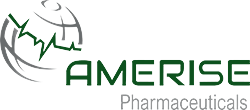
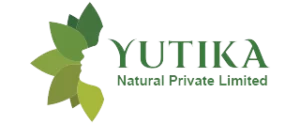
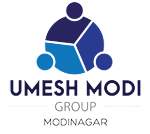
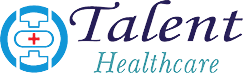
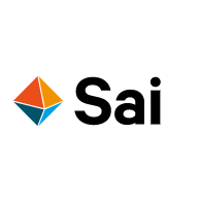
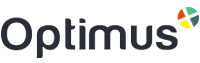
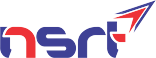
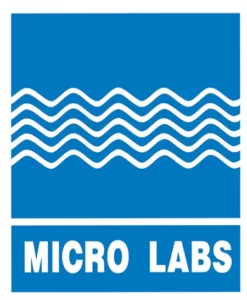
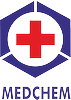
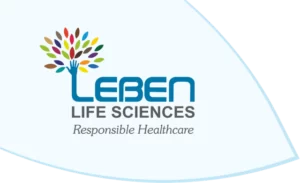
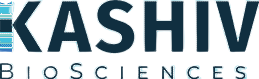
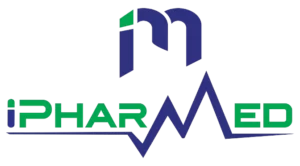
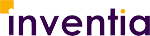
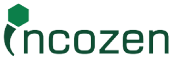
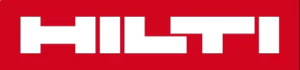
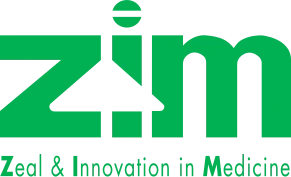
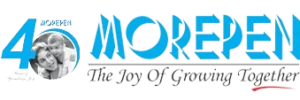
IITs, AIIMS, CSIR, Government and Private Institutes
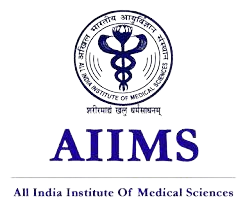
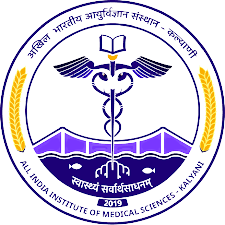
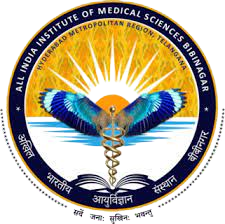
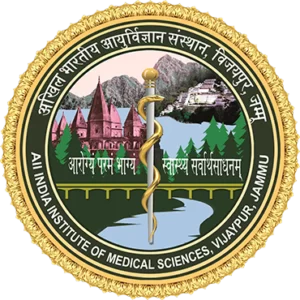
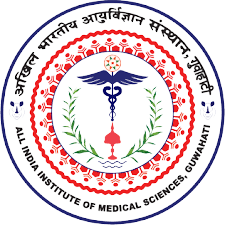
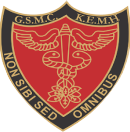
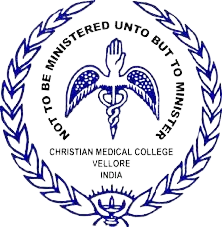
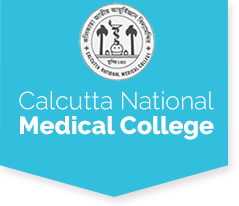
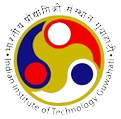
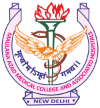
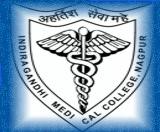
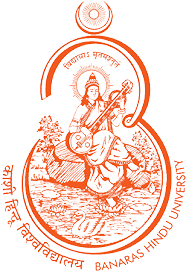
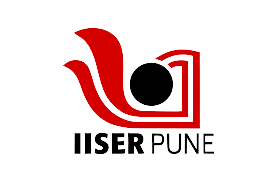
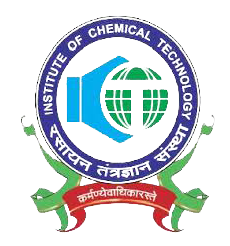
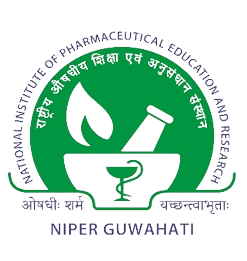
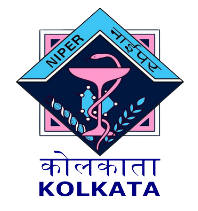
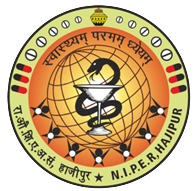
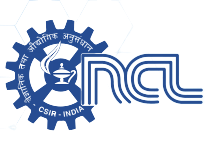
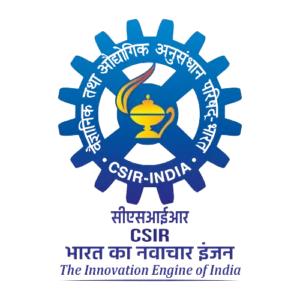
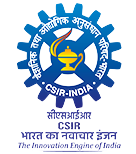
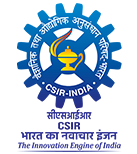
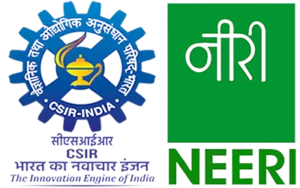
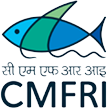
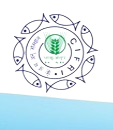

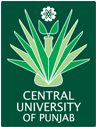

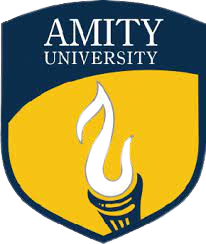
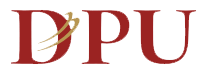
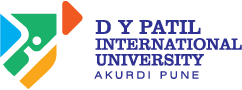
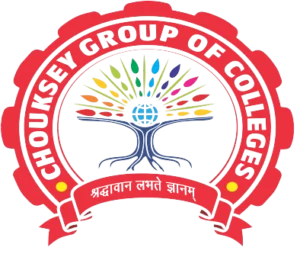
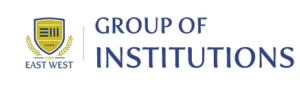
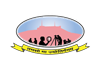
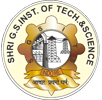
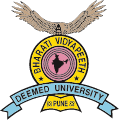
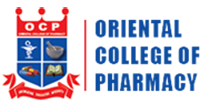
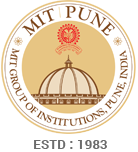
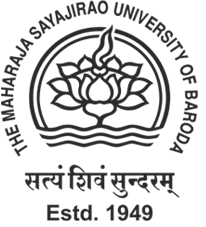

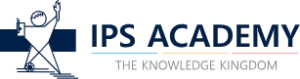
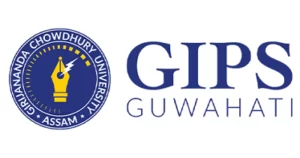
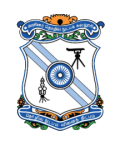
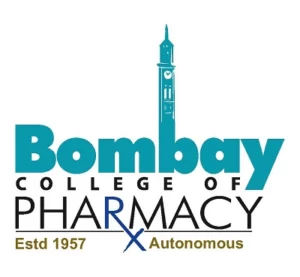
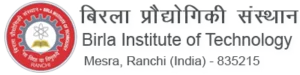
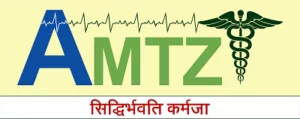
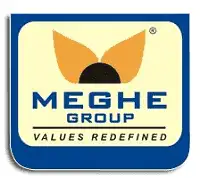
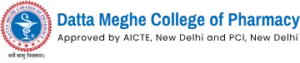
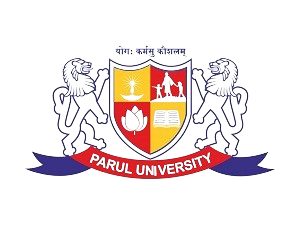
Related Products
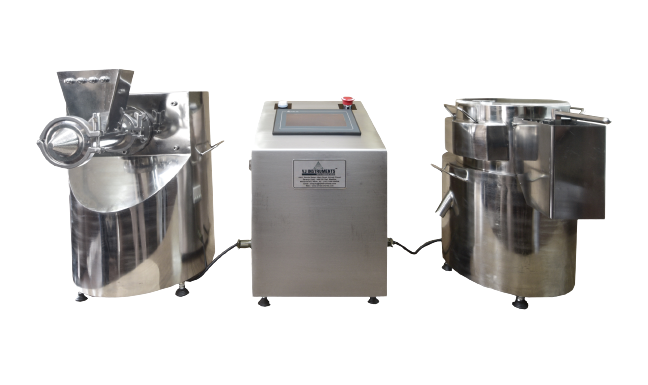
Lab-Scale Screw Extruder & Spheronizer Combo
VJ Instruments’ Lab-Scale Extruder & Spheronizer Combo Lab-Scale Extruder and Spheronizer Combo is a seamlessly
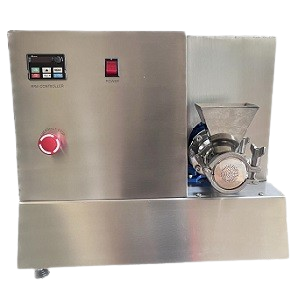
Lab-Mini Screw Extruder
VJ Instruments’ Lab-Mini Screw Extruder: Tailored Solutions for Pharmaceutical Pelletization Screw Extruders are versatile and
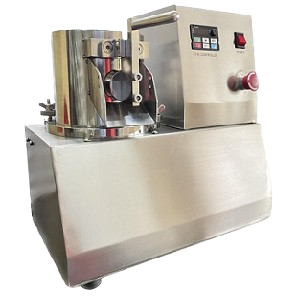
Lab-Mini Spheronizer
VJ Instruments’ Lab-Mini Spheronizer: Solutions for Pharmaceutical Spheronization Welcome to the world of pharmaceuticals and
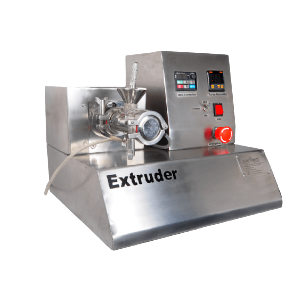
Hot Melt Extruder
VJ Instruments’ Hot Melt Extruder: Revolutionizing Pharmaceutical Formulations Welcome to VJ Instruments, your trusted source