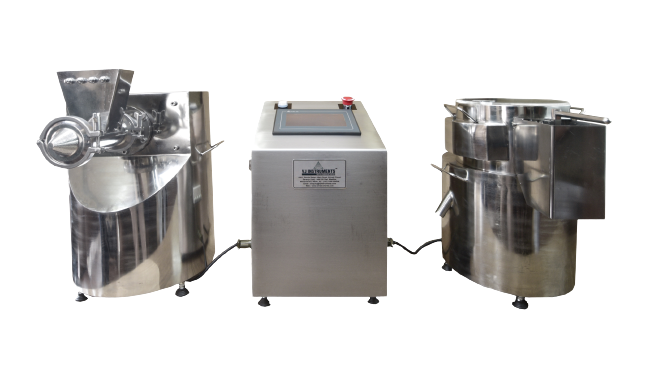
About Extrusion–Spheronization: A Comprehensive Overview
The extrusion–spheronization method has solidified its reputation as the cornerstone of pellet manufacturing. This ingenious process, initially conceptualized by Reynolds and later refined by Conine and Hadley, has been instrumental in the pharmaceutical industry since the early 1960s. The primary objective of extrusion-spheronization is to create consistently sized spherical pellets, which prove invaluable in the development of controlled-release solid oral medications with minimal excipient usage. A noteworthy advantage of this technique is its capacity to blend and formulate different drugs into a single dosage form, facilitating the simultaneous or sequential delivery of chemically compatible or incompatible medicines at specific locations within the gastrointestinal tract.
INTRODUCTION
The extrusion–spheronization method is the most popular method of making pellets. This process was first reported by Reynolds and by Conine and Hadley.
- Extrusion-spheronization is a pelletization technique developed in the early 1960s, and regularly used in the pharmaceutical industry to make uniform size spheres.
- It is beneficial for making dense granules for controlled-release solid oral dosage forms with minimum excipients.
- Pellets composed of different drugs can be blended and formulated in a single unit dosage form that facilitates the delivery of two or more chemically compatible or incompatible medicines at the same or different sites in the GI tract.
Advantages of Pellets
The pellets or beds produced by the extrusion-spheronization process offer several advantages over conventional drug delivery systems.
- Produce spheroids with a high loading capacity of active ingredients without producing extensively large particles.
- Dispersed freely in the GI tract, it maximizes drug absorption, reduces peak plasma fluctuations, and minimizes potential side effects and toxicity owing to the reduced dose and increased bioavailability.
- Produce uniform-size particles having narrow size distribution and good flow properties.
- Successive coating is applied to the spheroids because of their spherical shape and low surface area to volume ratio.
- Pellets also tend to avoid high local concentrations of bioactive agents, which may inherently be irritating anesthetic to the stomach.
The bulk drugs and excipients are converted into agglomerates by the process of Pelletization. The agglomerates formed by this process are small, free-flowing, spherical or semispherical units called pellets.
Extrusion and Spheronization is a involves four-step process:
- Preparation of the wet mass (Granulation)
- Shaping the wet mass into cylinders (Extrusion)
- Breaking up the extrudate and rounding of the particles into a sphere (Spheronization)
- Drying of the pellets
FORMATION AND GROWTH MECHANISM OF PELLETS
- Nucleation, coalescence, layering, abrasion transfer, and size reduction are the events that lead to the formation and growth of pellets.
- In nucleation, primary particles are drawn together to form three-phase air-water solid nuclei (Fig. 1A).
- The collision of well-formed nuclei to form larger particles is known as coalescence (Fig.1B).
- Successive addition of material on already formed nuclei is layering (Fig. 1C).
- Transfer of material from one particle to another without any preference in either direction is abrasion transfer (Fig. 1D).
- There are three size reduction mechanisms that indirectly affect the growth mechanism, particularly layering and, to some extent, coalescence. Well-formed particles may undergo size reduction due to attrition (Fig. 1E), breakage (Fig. 1F), and shatter (Fig. 1G).
PELLETIZATION TECHNIQUES
Depending on the type of equipment and processes selected, pellet formation and growth may occur in a number of ways.
Agitation: In agitation, finely divided particles are converted to spherical particles, upon the addition of appropriate quantities of liquid, by a continuous rolling or tumbling motion. The liquid may be added before or during the agitation stage. Pans, discs, drums, or mixers may be used to produce pellets for the balling process.
Compaction: Compaction is a form of pressure agglomeration in which drug particles or granules are forced together with or without formulation aids by a mechanical force to generate pellets of well-defined shapes and sizes. During compression, the granules/ agglomerates are prepared using dry or wet granulation followed by drying, and rearrange to form a closely packed mass. The particles are forced against each other at higher pressure, which undergoes elastic and plastic deformation. The dry powder mix is first agglomerated with a binding liquid in extrusion-spheronization. Then it is processed in the extruder to produce high-density extrudates. The extrudes thus formed are finally converted to pellets on a spheronizer.
Drug layering: Two methods that are important in Pelletization by layering method solution layering and solid powder layering. In powder layering, a binder solution is first sprayed onto the tumbling inert pellet, and then the powder is added. The tumbling moist inert pellet in the rotating pan or disc picks up powder particles and forms layers of small particles that adhere to each other. As the additional binding liquid is sprayed, the layering of more powder on the pellet continues until the desired pellet sizes are obtained.
In the case of the solution or suspension layering process, the drug substance is dissolved or suspended in the binder solution (solution/suspension) and sprayed onto the seeds, often inert pellets, forming a uniform and smooth surface. Spreading depends on the droplet wetting characteristics, the wettability of the material, and droplet dynamics.
Globulation: In the globulation process, liquid materials like melt, solution, or suspension are atomized to generate spherical particles or pellets. During spray drying, the atomized droplets are contacted by a hot gas stream, and evaporation of the liquid is initiated. Evaporation involves simultaneous heat and mass transfer and depends on the air’s temperature, humidity, and transport properties surrounding the droplet. During spray congealing, the atomized droplets are cooled below the melting point of the vehicles. A critical requirement in this process is that substances should have well-defined melting points or small melting zones
EXCIPIENTS USED IN PELLET FORMULATION
Pellets consist of various formulation aids such as
- Filler/Diluent: To add bulk (dibasic calcium phosphate, lactose, microcrystalline cellulose, starch, sucrose),
- Binders: To bind powders and maintain pellet integrity (hydroxypropylmethylcellulose, polyvinylpyrrolidone)
- Lubricant: To reduce the coefficient of friction between individual particles or between the particles and the surfaces of the processing equipment (magnesium stearate)
- Separating Agent: To promote the separation of pellets into distinct units during a pelletization process (talc)
- Disintegrants: To promote the disruption of pellets (croscarmellose sodium, sodium starch glycolate),
- Spheronization Enhancer: To facilitate the production of spherical pellets (microcrystalline cellulose)
- Release Modifier: To get the modified release from the pellet formulation (ethylcellulose, shellac)
STEPS AND EQUIPMENT USED IN EXTRUSION–SPHERONIZATION
EXTRUSION:
- The extrusion operation is an integral part of the overall spheronization process in which the wet powder mass is forced through the narrow orifice to produce extrudates.
- The dimension of orifice in terms of radius and length may vary from system to system depending on the physical characteristics of the materials to be extruded, method of extrusion.
TYPES OF EXTRUDERS:
Extrusion is performed using four main classes of extruders:
- Screw Extruder
- Sieve Extruder
- Basket Extruder
- Roll Extruder
- Ram extruder
TYPE OF EXTRUDER | MECHANISM | FEATURES |
SCREW EXTRUDER | Utilizes a screw to develop the necessary pressure to force the material to flow through uniform openings | a.Axial: Screen is placed at the end of the screw, perpendicularly with the axis of the screw (Fig 1). b.Radial: Screen is placed around the screw, discharging the extrude perpendicularly to the axis of the screw (Fig 2) |
SIEVE EXTRUDER | A rotating or oscillating arm presses the damp material through a sieve. | Extrude falls vertically from the sieve plate |
BASKET EXTRUDER | Similar to sieve extruders, except that the sieve or screen is part of a vertical cylindrical wall. | Extrude formed in the horizontal plane |
ROLL EXTRUDER | Roll extruders operate by feeding material between a roller and a perforated plate or ring die. | Type 1: A ring rotates around one or more rollers installed inside the cylindrical die chamber, each of which rotates on its stationary axis. Type 2: The roller or rollers are mounted on the outside of the ring die and material is fed from a hopper, occasionally with a screw, into the region between the roller and the die. Type 3: Rollers are positioned above and roll along the surface of a flat, stationary die plate |
RAM EXTRUDER | A piston riding inside a cylinder or channel is used to compress material and force it through an orifice on the forward stroke | Extrusion forces recorded with the ram extruder are always greater, and force necessary to extrude the wet mass through the ram extruder decreases as the quantity of added water increases. |
The two most prevalent and effective forms of wet mass extrusion are Screw Extrusion and Screen Extrusion for pharmaceutical, food, and other industry.
Screw extruders
The central screw of the extruder operates with a power supply, a feeder (for material), and a barrel. The barrel encases the screw. The screw pushes the material i.e. pressure is applied to the material and it is forced along the axis towards the end (a shaped hole) called the die that shapes the product. The product, now called an extrude, exits the extruder through the die, where its texture changes.
Twin-screw extruders can be co-rotating or counter rotating. These extruders can be made to process a much wider variety of materials — polymers, additives and fillers — because the screw profiles can be much more easily changed and they are more versatile than single screw machines because the melted material is worked between the two screws.
Counter rotating twin-screw extruders are used to produce continuous hollow profile shapes such as pipe shape or rectangular shape. Counter rotating means that the two screws rotate in opposite directions which forces the material to the walls of the barrel as it passes through the barrel driven by the two screws.
Co-rotating twin-screw extruders used for production of molding compound have inter-meshed screws and the material soften primarily by the action of the two screws working the material between the screws
BASKET OR SCREEN EXTRUDER
- A basket Extruder is the lower-pressure method of wet extrusion combined with moderate sheer. Basket extruders offer a very versatile means of wet extrusion to form granules from 0.5 to 5.0 mm in diameter. They produce consistent extrudate from wetted powders at the laboratory through multiple ton-per-hour extrusion capacities. In the upper chamber of basket extruders, the counter-rotating internal breaker bar system breaks larger clumps of wetted feed material. Along the gravity, the wetted material massed into the bottom extrusion rotor arms, densifying the material and extruding it through the screen basket. Formed extrudes that have a stable structure with a large surface area are discharged without damage, providing the optimum flexible properties for spheronization.
PERFORATED COATING PAN
- It consist of perforated drum that is rotated on its horizontal axis in an enclosing housing.
- In the acceclo-cota an hi-coater system, the drying air is directed in to the drum, is passed through the tablet bed and is passed through perforation in the drum.
- The hi-coater introduce drying air through hallow perforated ribs located on the inside periphery of the drum.
- As the coating pan is rotates the ribs dip in to the tablet bed and the drying air is passed up through and fluidized the tablet bed.
FLUIDIZED BED COATING
- Highly efficient system.
- Fluidization of tablet mass is achieved in a columnar chamber by the upward flow of drying air.
- The air flow is controlled so that more air enters the centre of the column causing the tablet to rise in the centre.
- The movement of the tablet is upward through the centre of the chamber.
- Then all toward the chamber wall and downward to re-enter the air stream at the bottom of the chamber.
- Coating solution is applied from the spray nozzle located at the bottom of the chamber.
TWIN SCREW EXTRUDER CONFIGURATION
SPECIFICATION
Max. Speed : 1000 rpm
Speed Range : 10 to 1000 rpm
Dimensions (L x W x H) : 1750 x 610 x 1220 mm
Barrel Length : L/D-40:1 L/D
Weight (Metric) : 350 kg
Pressure : 150 bar
SPERONIZATION
The spheronization machine consists of a friction plate and a rotating shaft, spinning at high speeds fitted on the bottom of the bowl shape cylinder. In the spheronization process, a friction plate is a significant part and plays an important role. A friction plate consists of a grooved surface that cuts the cylindrical extrudes into segments. The segmented material collides with the wall of the spheronizer due to centrifugal force and is thrown back to the friction plate. This action continues, Collison rounding the segments into the sphere form. In the case of obtaining good quality pellets, the friction plate and the diameter of the friction plate plays an important parameter.
PARAMETERS INFLUENCING FINAL PELLET QUALITY
FORMULATION PARAMETERS
- Moisture content
- Granulating liquid
- Excipients
- Drugs
PROCESS PARAMETERS
- Extrusion speed
- Extrusion temperature
- Spheronizer load
- Spheronization time
- Spheronization speed
- Drying method
EQUIPMENT PARAMETERS
- Mixer
- Extruder
- Friction plate
- Extrusion screen
ADVANTAGES
- Agglomerates of material with a uniform and controlled size
- Producing small particles with a high surface area to volume ratio
- The optimization of flow characteristics
- Producing the optimum shape for coating
- To facilitate the mixing of non-compatible products
- To improve the appearance of powder or granulated materials
- To improve the ability to reproduce the same physical properties of packing beds and columns
- To improve the hardness and friability of granules
- To increase the density of granules
- To improve accuracy in dosage control
- To improve the high speed handling of materials
- To remove dust hazard
- To simplify the handling of difficult material
- To simplify and increase speed of processing
DISADVANTAGES
- High initial or setup cost
- High compressive force required
- Screw mechanism can exert a high pressure on the material, generating excessive friction and heat as the wet mass passes between the screw and barrel.
Enhancing Heterogeneous Catalysts Through Extrusion: Synthesis, Structure, and Performance Optimization
When discussing heterogeneous catalysts in the context of extrusion, it’s important to highlight how extrusion can be specifically employed to enhance the synthesis, structure, and performance of heterogeneous catalysts. Here’s a more focused exploration of the intersection between heterogeneous catalysts and extrusion:
Uniform Dispersion: Extrusion enables the homogeneous mixing of catalytic precursors, supports, and promoters, leading to a well-dispersed active phase within the catalyst matrix. This uniform distribution is crucial for maximizing catalytic activity and selectivity.
Tailored Structure: The controlled shaping and structuring capabilities of extrusion allow for the design of catalysts with specific morphologies and architectures. For example, catalyst pellets, extrudates, or monoliths can be fabricated with precise dimensions and pore structures tailored for optimal mass transport and reaction kinetics.
Enhanced Surface Area: By incorporating porous materials or additives with high surface area, extrusion can increase the accessible surface area of heterogeneous catalysts. This heightened surface area provides more active sites for catalysis, resulting in improved efficiency and reaction rates.
Integration of Nanomaterials: Extrusion facilitates the incorporation of nanomaterials, such as nanoparticles or nanofibers, into the catalyst structure. These nanoscale additives can enhance catalytic performance by providing high surface area, promoting mass transport, and facilitating interactions between reactants and active sites.
Mechanical Strength: Heterogeneous catalysts produced through extrusion often exhibit enhanced mechanical strength and stability. The compaction and alignment of precursor materials during extrusion contribute to the formation of robust catalyst structures capable of withstanding harsh reaction conditions and mechanical stresses.
Scalability and Process Control: Extrusion offers scalability and process control advantages, allowing for the continuous and reproducible production of heterogeneous catalysts with consistent properties. This is particularly advantageous for industrial applications where large quantities of catalysts are required.
Tailored Functionality: Extrusion provides a platform for the synthesis of hybrid catalysts with tailored functionalities. Different materials can be incorporated into the catalyst matrix to impart specific catalytic properties, selectivity, or resistance to deactivation.
In summary, the integration of heterogeneous catalyst synthesis with extrusion technology offers numerous advantages for optimizing catalyst performance, structural properties, and process efficiency. This approach holds promise for advancing catalytic processes in various industries, including petrochemicals, environmental remediation, and renewable energy production.